Mining flowsheets can take many different routes, but more often than not they begin with drill and blast. Optimizing blasting outcomes can thus play a critical role in determining overall mine efficiency. North American Mining discussed current and future blasting best practices with experts from explosives providers and technology suppliers.
By Jonathan Rowland
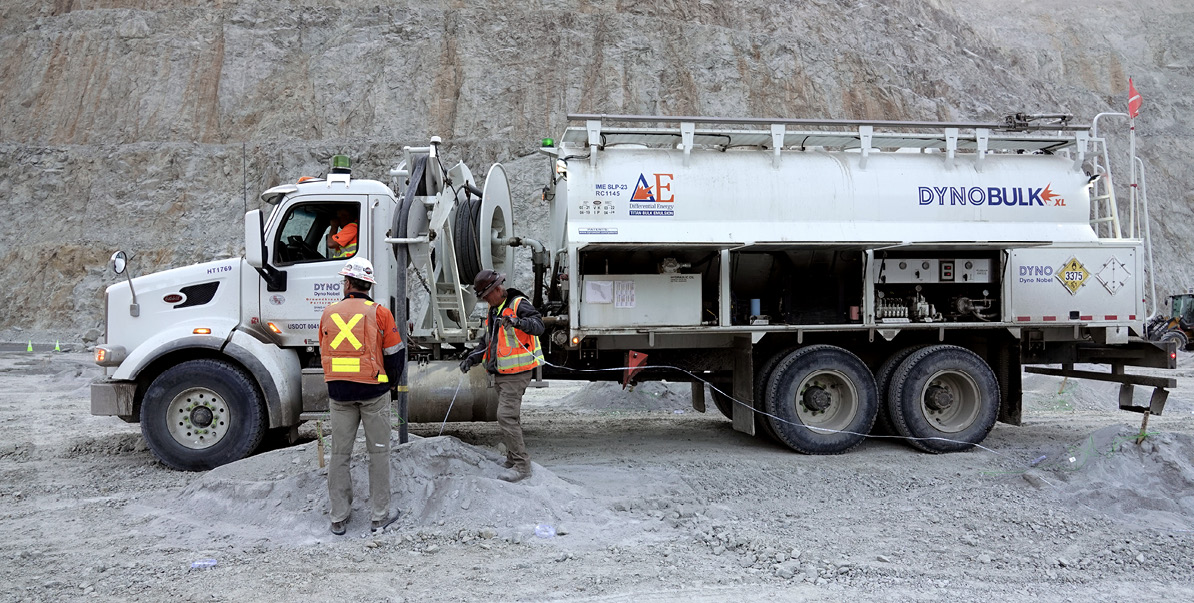
Drilling and blasting are “key functions in opencast mining, directly affecting operational efficiency, products costs, and long-term success,” said Mark Roberts, manager, Global Strategy at mining technology company Maptek, starting off our discussion on surface mine blasting practices. It was a discussion that began by outlining some of the major challenges and practices that reduce the efficacy and efficiency of blasting operations.
“Time is always of the essence,” contributed Franky Botha, head of Strategic Partnerships at AECI Mining, which manufacturers explosives, initiating systems and blasting solutions for the mining industry. “Most mines have a specific scheduled blasting time, which has a lot to do with the impact of blasting noise and vibration on local communities. Production pressures often result in drills still being on the bench while explosives trucks are waiting to charge blast holes. Any delays in the sequence will put more pressure on workers to complete the task on time, but pressure can result in rushing – and rushing has safety implications.”
Time pressures and regulations were also picked up by Adam Aubin, senior manager, Technical Solutions, at blasting solutions provider, Orica. “A practice not used often today is to let the explosives sleep overnight. Sleeping blasts would allow for larger blasts to be loaded and fired creating more uniform fragmentation and increasing the efficiency of the mine; however, stricter regulations and production pressures now make this practice uncommon. There are also challenges around lighting, which typically happens in the early afternoon in wet seasons and forces the mine to load and blast on the same day, minimizing the blast size.”
Other practical challenges revolved around the “execution of best practices on the bench,” added Mike Kotraba, general manager of DynoConsult, the explosives and blast consulting team at Dyno Nobel. These include:
- Getting the blast pattern on-grade.
- Drilling blastholes in the correct location and to the correct depth.
- Loading the pattern to the actual designed powder factor.
- Optimizing timing to achieve the goal of the blast (fragmentation, wall control, spill-over control, etc.).
“Nearly all mines struggle with these things,” continued Kotraba. “Improvements in equipment automation and GPS controls help but have not fully solved the inconsistencies seen in pattern execution on the bench, day in, day out.”
Which brought the discussion back around to Roberts: “in the fast-paced mining environment, the latest information is crucial to informing decisions. Technology is available to produce this information; the challenge is in using it effectively. Efforts toward continuous improvement in blasting practices must concentrate on timely analysis and application of crucial data from the information stream, such as variable geology and structure, drilling conditions, and unexpected issues.”
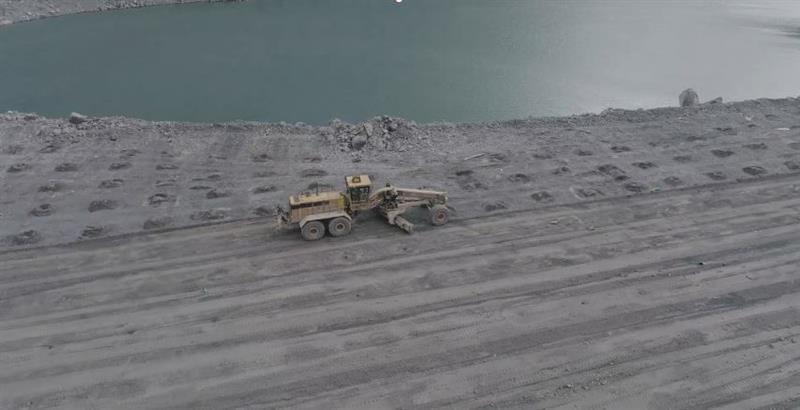
Supporting optimized blast design
Roberts continued the discussion to address issues in blast design, noting that “traditional or static blast design is often based on conservative parameters to try to account for variability.” This is opposed to “adaptive design, which recognizes that geological and operational conditions on the bench will vary. Adaptability in blast design and execution processes enables mines to improve compliance with mine designs, which is a significant contributor to overall blast performance.”
According to the Maptek executive, the key elements underpinning adaptive blast design, execution, and reconciliation processes are “real-time data integration combined with dynamic design parameters for drill patterns, primer configuration, explosive type, stemming and delay timing. These must be considered together to optimize energy distribution, which is critical for environmentally sensitive blasts that demand greater attention to detail for control. Routine blast monitoring and post-blast analysis are also fundamental to understanding actual outcomes against planned design, and applying this information back into the design process for the next blast.”
The adaptive approach allows engineers to “readily incorporate automatic, immediate design parameter adjustments into their designs and make these visible to blast crews, based on real-time hole conditions and variability in execution on the bench,” concluded Roberts. The final element for adaptive blast design is thus a “team approach between mine planning and operations to ensure effective communication and insights are shared and understood. This should also include contractors where they are responsible for activities like explosives loading.”
DynoConsult’s Kotraba also picked up this theme of collaboration and adaptability. “Highly trained mine planning and blasting teams are now working with their explosives supplier’s technical teams to implement more complex pattern designs. Customizing the explosive load by borehole, based on the unique geologic features encountered during drilling, is starting to become a best practice, along with optimizing blast timing to achieve the desired pattern outcome, whether it is a specific particle size distribution or wall/vibration control.”
Blasting and ESG
As blasting in inherently hazardous, mines have “always considered ESG factors,” said AECI Mining’s Botha. “Yes, by giving it a name, mines may have become more diligent but, in my experience, explosives suppliers and mine operators have collaborated very well over the years to ensure blasting has minimal impact on ESG.”
Typical ESG considerations related to blasting include:
- Environment: noise, dust, blasting fumes.
- Social responsibility: vibration, airblast, noise, and flyrock.
- Governance: the control of explosives and initiating systems is “well entrenched by the governing bodies and adherence is excellent,” said Botha. “Essentially, explosive suppliers have a cradle-to-grave policy and therefore make every effort to prevent explosives from getting into the wrong hands. This is also the case for end-users.”
Mines have “become more sensitive to ESG issues,” agreed Orica’s Adam Aubin. “Mines want to reduce blasting fumes, flyrock, dust, air overpressure (noise), blasting vibrations, and nitrate levels, not only for compliance with their neighboring communities and the local regulations, but also for the environment as a whole.”
Mines are also becoming more aware of blasting “within the complete comminution process, including optimizing the energy required to process material,” added Maptek’s Roberts. “Strategic tools allow better decisions to be made, taking into account the history of blasting at the site and matching it to the processing outcomes. For example: identifying inefficiencies due to drill set-up errors will help reduce oversize rock and poor blast digability, and can contribute to continuous improvement in material recovery and overall performance.”
“The explosives industry has and will continue to contribute to many of the historical mining advances as part of the total mining value stream,” concluded DynoConsult’s Kotraba. “One of the biggest current ESG challenges is to lower lifecycle greenhouse gas emissions as part of efforts to decarbonize the mining industry. The explosives industry is supporting this by focusing on less carbon-intensive and more fuel-efficient methods for transportation of explosives (e.g., rail vs. truck where possible), as well as moving toward sustainable and renewable oil and fuel phase sources in formulations.”
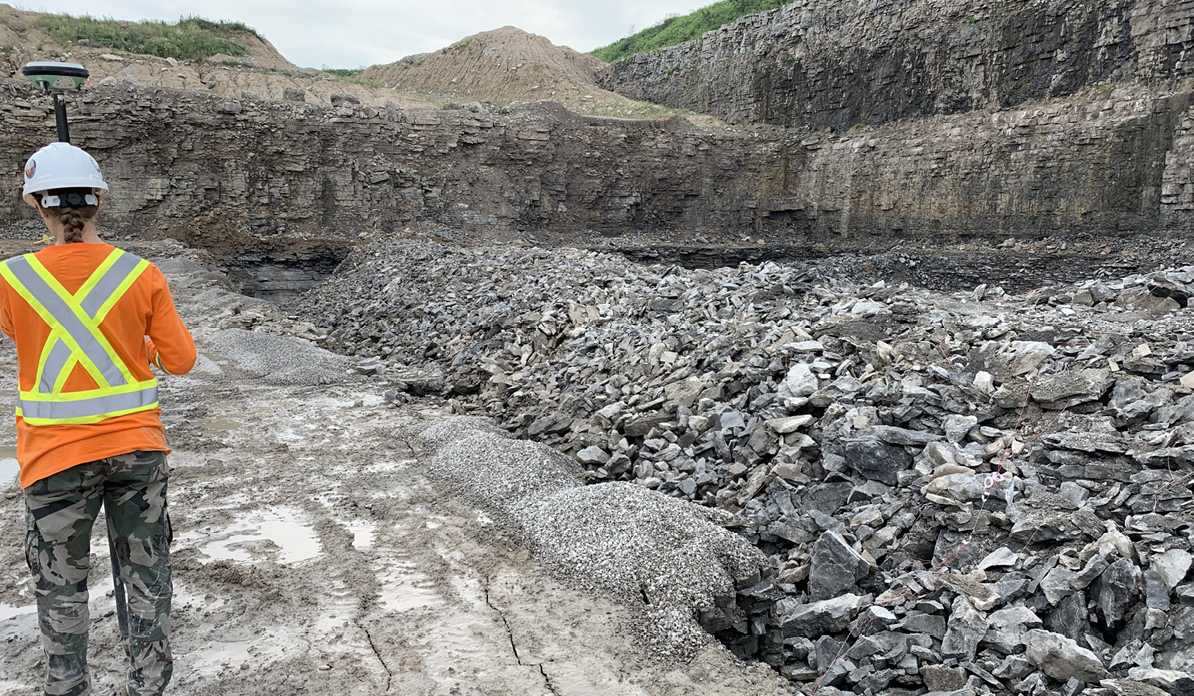
Latest developments in blasting solutions
Heightened focus on ESG – and decarbonization in particular – has also “prompted explosives suppliers to look at how they can assist customers in achieving their sustainability goals,” continued Kotraba. These developments include “new explosive emulsions with higher energy content and innovations in electronic detonators that provide a higher level of safety, lower misfire potential, and optimized timing flexibility. These all contribute to higher blast yields with little or no increase in pounds of explosives used.”
“Explosive formulations are being modified to greatly reduce or eliminate toxic blasting fumes and nitrate levels in the water,” said Remi Proulx, senior engineer, Technical Solutions, at Orica. “Other innovative lower-density explosive formulations are being used to minimize the blasting vibration levels, due to the reduced maximum instantaneous charge. Electronic detonator technology is also being used to time blasts to reduce blasting vibrations at a point of interest.”
“Wireless initiation technology provides for the ability to reduce the number of blasts while increasing the blasted rock mass per month,” added Proulx. “It can also help reduce flyrock: with wireless initiation it is easier to cover blast holes by driving over loaded blastholes and dumping fill material, without risking unplanned detonation of misfires due to the lack of wires. Wireless initiation also allows effective dust control as the water truck can wet the blast much closer to blast time due the absence of wires on the surface.”
“Electronic initiation enables blasters to have much more control over the blast as well as the blast outcome, i.e. fragmentation, muckpile, fly-rock, etc.,” agreed Botha. “Wireless electronic detonators also have the objective of removing people from the bench and pave the road for more autonomous mining. Storing explosives is also becoming safer with bulk emulsion explosives formulated to only become active when in the blast hole.”
Droning on?
Another technology that has recently made its way into the mine – as well as everywhere else – is unmanned aerial vehicles, or drones. These “essentially enable fast and quick data collection, while keeping people safe,” explained Michael Blake, a product manager at drone manufacturer Flyability. “You can use that data as part of your record of mine progress, as well as tracking resources (e.g., what does a blast with x units of explosives look like at this site). It’s also good for measuring blast efficacy.”
The Elios drone from Flyability has typically been deployed in underground mines, where terrain is particularly challenging; however, this “doesn’t discount its use in surface blasting operations”, continued Blake. “You can use LiDAR scans from the Elios for pre-blast planning and checking the layout of charges. After a blast, the drone can be flown to survey the area for a cut-and-fill volumetric comparison. Drone-gathered data can also be used to produce a to-build model that enables drill rigs to see clearly where to drill.”
Used in this way, drones can empower faster decision-making and data collection, as well as record-keeping. This helps make the overall process more efficient and safer, reducing human entry onto the bench, and enabling machinery to keep operating without pauses.
In terms of advice for mines looking to include drones, there are “several steps to take,” said Blake. “Firstly, it is a good idea to know the drone regulations in your area. If a certain size drone requires specific licenses, that could affect how much you are able to use a drone on the surface. There will also be strict rules when near an active airport.
“Similarly, drone selection should be based on the specific project requirements: if you want high aerial data for mapping, you may not want a cage drone. However, for work that involves surveying blast areas and hazard exposure, a cage drone, such as the Elios, would suit you well. It is also important to ensure pilots are well trained and comfortable with their drones, while carefully maintaining the drones and keeping up-to-date with the latest best practices. For example, the US recently introduced a requirement for all drones used outdoors to have a remote ID (RID). As a result, the Elios was adapted to comply with this rule.”
A drone – or even a fleet of them – “can be a game-changer for a mine,” concluded Blake. “A correctly used drone will make a site safer, while gathering high-quality data that will assist the mine work faster and more efficiently, and providing detailed records of work. But as with any technology, if you don’t do your research, engage in training, or keep your device in good condition, you may not get as much out of it as you wish.”
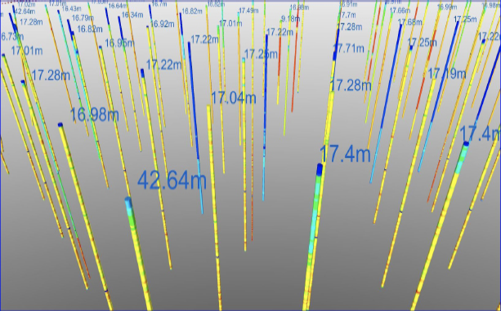
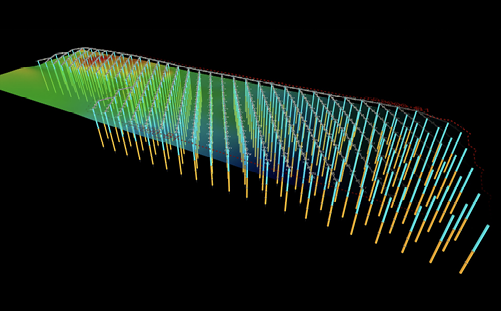
Maptek Blastlogic provides an adaptive design and reconciliation platform. Charge rules can back-calculate maximum instantaneous charge (MIC) of each hole relative to unlimited sensitive locations. The MIC can then be used to develop a user-defined deck configuration and, once programmed, the plan can be regenerated autonomously based on current hold conditions. Photos: Maptek
What’s next?
“I see two main areas for development in the blasting sector in the coming years,” said Orica’s Adam Aubin. “More advances using wireless initiation technology, such as double bench mining and mine schedule flexibility, will become household names. Secondly, 4D emulsion technology, combined with digital solutions, will allow mines to match the relative bulk strength of the explosives to the geology on the bench as recorded by drilling digital solutions tools. This has the potential to become the new standard in explosives loading.”
“Advancements in equipment monitoring and automation, data gathering, and data processing are all helping mines move from lagging indicators to leading indicators or real-time indicators to guide decision-making during a shift,” added DynoConsult’s Kotraba. “Just-in-time data monitoring and processing will allow changes in ongoing mining and processing activities to be made and optimized on the fly, throughout every shift, leading to more productive mining and sustainable downstream processes.”
Maptek’s Roberts also focused on the benefits of new digital technologies. “Current blast design tools require engineers to employ a brute force approach to generate scenarios that allow them to optimise competing blast objectives. The challenge is particularly difficult considering the need to take a multitude of interrelated factors into account, as well as weaknesses in simulation models, which are often siloed and based on non-current data from infrequent, large-scale reviews.”
According to Roberts, artificial intelligence-based solutions – such as Maptek BlastMCF, which is due for release in 2024 – have the potential to change this by automating the creation of optimized and detailed blast designs, encompassing drill pattern, per hole charging, and timing.
“With the foundational design established, engineers can dedicate more time to fine adjustments, a critical aspect given the extensive nuance and complexity inherent in drill-and-blast operations,” Roberts explained. “We believe the ability to perform more scenario analysis for rapid validation and verification of design concepts will be highly valued by mine planning teams. This forward-looking approach aligns with the evolving understanding of blast performance factors and emphasises the importance of achieving greater control through enhanced engineering practices.”
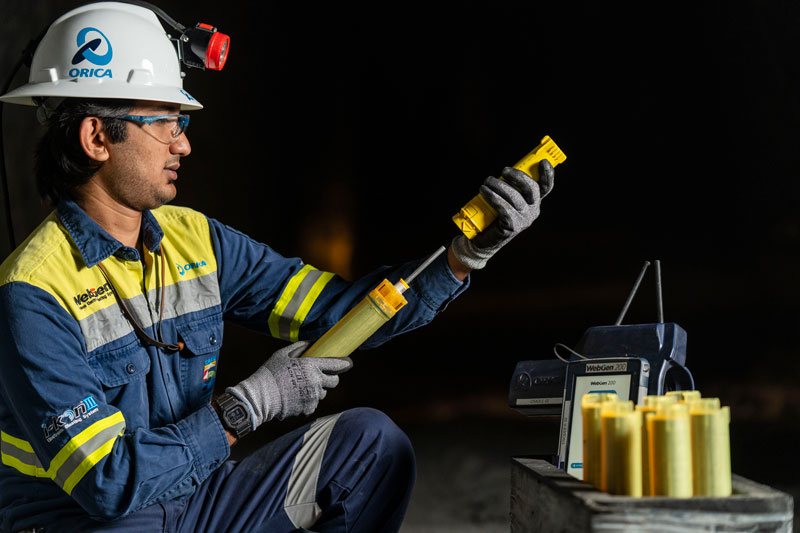
Some final advice
“Chemical energy remains the cheapest form of comminution,” offered AECI Mining’s Botha. “Miners often go for the cheapest explosives solution, but experience has shown that downstream efficiency improvements far outweigh the cost of explosives. Payback is immediate and comes in various forms, ranging from basic cost savings to an increase in production rates.”
Kotraba echoed Botha’s point, asking miners to first “keep in mind the mining and processing value chain starts with drilling and blasting. Minor changes here can lead to significant value adds (or value losses) the further you move down the mining and processing value chain. Focus on best practices. If you get those right, you will improve both operational efficiency and sustainability.”
He then also turned to the theme of cost: “explosives are an investment, so an operation’s goal should be to maximize its explosive return on investment. To do so, you need to know what outcome you want from your explosive, so that each blast is designed and executed to achieve that outcome. Most mines spend a lot of money on explosives, so work with your explosives provider to get the most bang for your buck with each shot you shoot!”
Collaboration was also on the mind of Mark Roberts of Maptek, as he concluded the discussion: “partnerships between technology providers like Maptek, original equipment manufacturers, and explosives suppliers, are the ideal approach to deliver end-to-end optimization of drill and blast.”